Madison Lean Six Sigma Certifications for Businesses
Contact Us
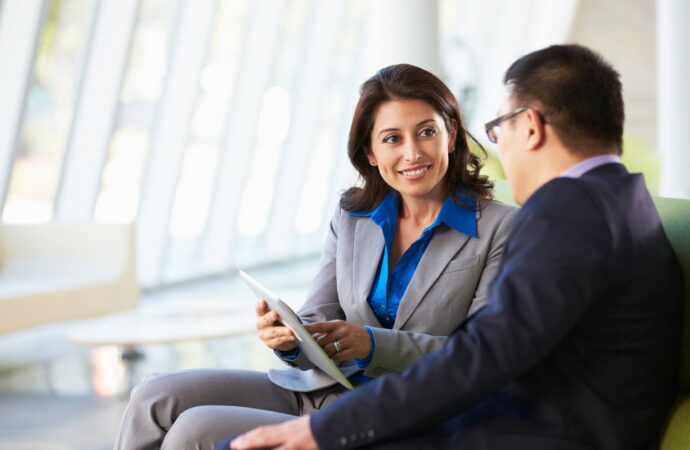
Lean Six Sigma has been a methodology that, contrary to what many believed, has been growing in popularity due to its versatility and ability to help any individual or company with continual improvement, making it a well-known and requested method in the USA, which is why it isn’t strange to see how the LSS industry has been growing exponentially. We at Lean Six Sigma Curriculum for Madison High School Students of Wisconsin understand how LSS has changed over time. As experts who have been working in the area and industry for over a decade, we can tell you three main things:
- LSS is a great methodology that covers all areas of continuous improvement, which is why, besides manufacturing, more industries have started implementing it, leading to growth in the industry.
- Practitioners are valuable, which made more people decide to get trained and certified in different levels of Sigma as a result.
- The methodology is unique, and as a company that helps others, we guarantee you it is worth the investment and time you decide to pour into it.
But before taking the step with the last thing mentioned, it is common to review the history of the industry to get a better idea of how it has evolved over time.
It is important to understand that LSS has its roots in the United States. LSS was established when American industries were faced with Japanese products and manufacturing and how the latter were surpassing the USA and leaving most of the products out of the market.
LSS allowed the USA to implement methods that focused on customer satisfaction and great results in order to compete with Japan’s industry.
Kaizen, which is continuous improvement and customer satisfaction-focused, has been a huge help to Japan’s manufacturing industry and influenced the LSS method that originated in the 80s.
LSS was able to increase production and efficiency and place Japanese companies below ours. Better products and services were being produced, and the clients were satisfied.
Six Sigma and Lean were two methods that led to Lean Six Sigma. Combining these two methods created a system that could increase performance and satisfaction.
It is very popular because it is universally adaptable and can be used by anyone if they have been provided with proper training and can prove that the training has been done correctly.
Lean Six Sigma can reduce wasteful activities. Practitioners and individuals need to adapt the structure and principles of Lean Six Sigma to their industry to achieve desired results.
Reduce the number of steps and focus on what is most important. This will simplify the process and improve performance, even if one person is working on the task.
It’s More Useful Than You Would Expect
Let’s take a moment to look at the methods that have led to the LSS industry.
As an individual approach to industrialization Lean has been a powerful tool since then and was one of the key methods that enabled LSS.
Businesses have used Lean principles to improve productivity, meet customer demand, and improve their bottom line. This independent method, which has been in existence since the 1940s and greatly improved LSS methodology, is not something that should ignore when considering LSS as the whole methodology.
Six Sigma, which is also known for continual improvement, waste reduction, and problem-solving, was the second method that made LSS possible. It is a key component of the DMAIC’s emphasis on finding solutions and identifying problems.
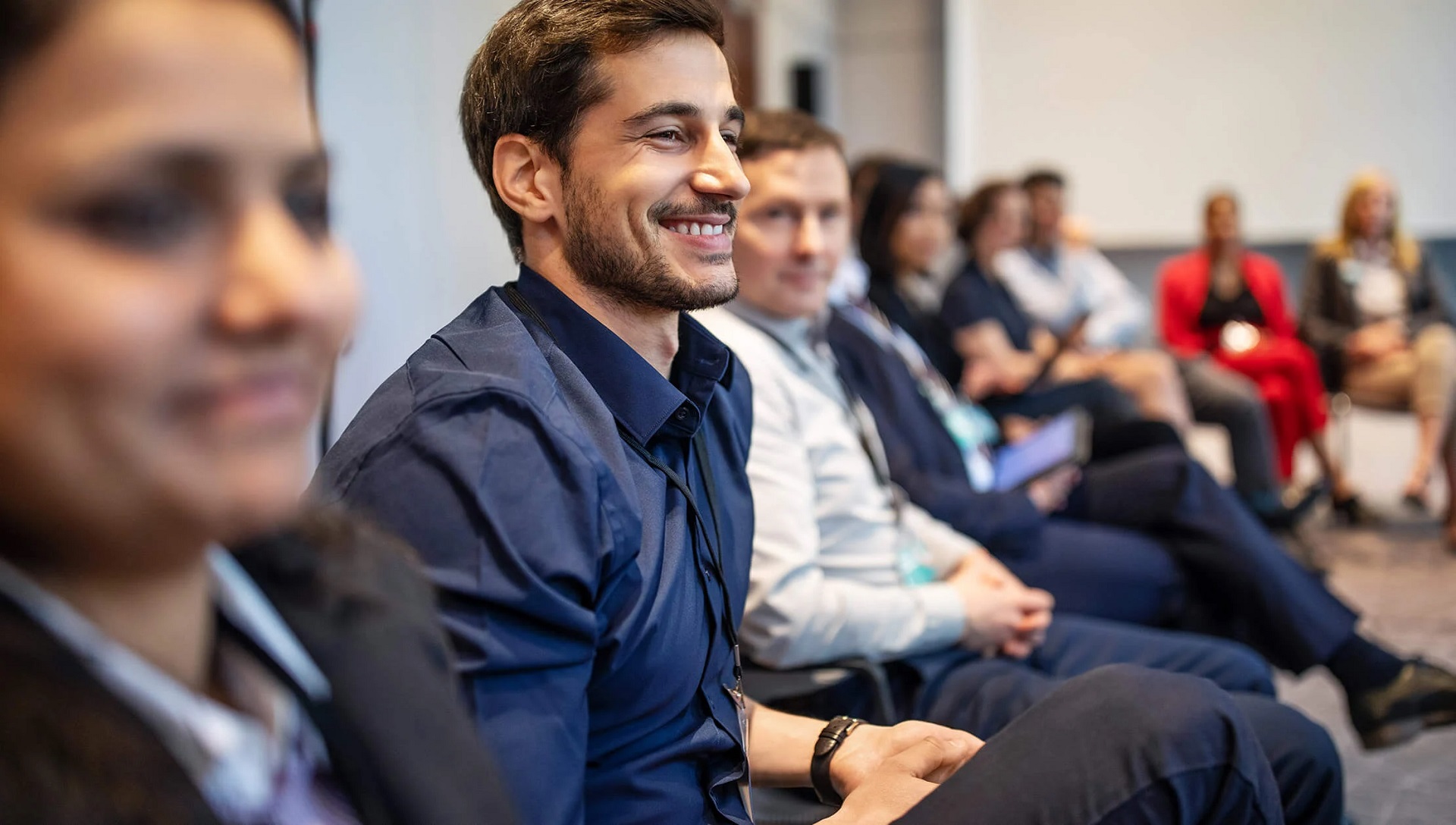
Six Sigma can improve manufacturing but can also be used for measuring, analyzing, and improving different elements. Many industries use Six Sigma to improve their quality control and control processes so that they can offer better services.
Six Sigma and Lean have been popular tools for improving performance since their introduction to the USA’s automobile industry.
America’s Lean Six Sigma industry grew because people were looking for solutions to their problems. Practitioners began to implement it in every system and process they could to ensure that companies and organizations are moving toward continuous growth since it involves the best of the previous methodologies while still adding more value in terms of quality, performance, and waste reduction.
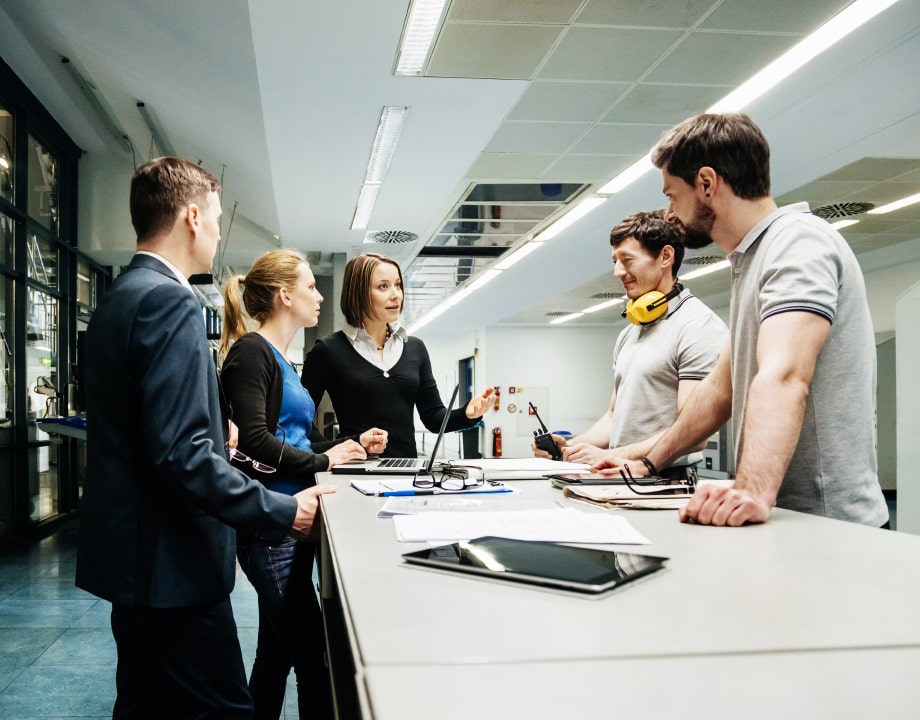